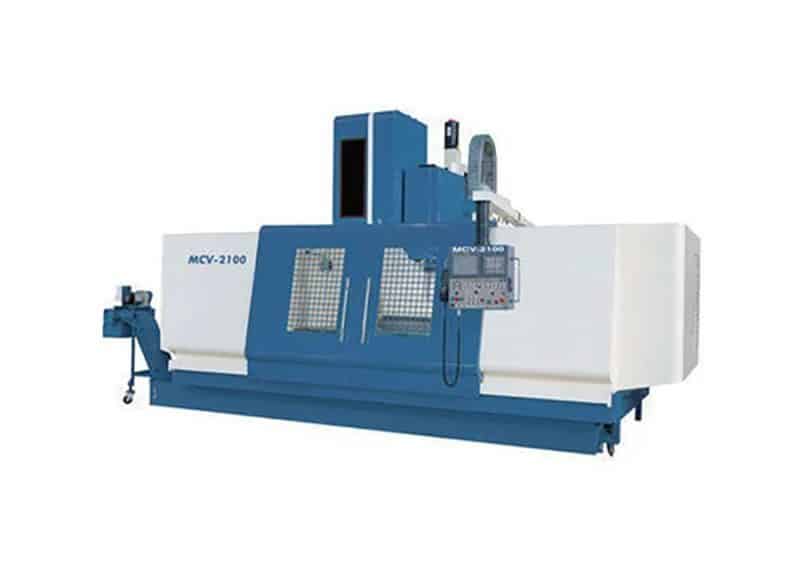
At Minland Machine, we’re prepared for the diverse needs of our clients, whether they’re in pursuit of high-speed precision or heavy-duty machining capabilities. We stand at the cusp of innovation, equipped with an arsenal of state-of-the-art milling machinery and advanced tooling solutions to meet those demands.
Read on to learn more about the differences between two of our mills, their capabilities and how Minland Machine is poised to partner with you on your next project.
The Duality of Machining: Box Way vs. Roller Guides
For those unfamiliar with milling machinery, the choice between box way and roller guide systems represents a fundamental decision. Box way machines, characterized by their heavy-duty gearboxes and iron construction, offer unparalleled grunt and durability. These machines are designed for deep cuts, higher feed rates and the kind of laborious tasks that demand more from both the machine and material. Yes, they come with a higher price tag, but the investment is justified through their performance, longevity and the sheer quality of work they produce.
Conversely, roller guide systems exemplify the pinnacle of speed and efficiency in modern machining. While less expense than box way options, they don’t compromise on precision, making them ideal for applications requiring high-speed spindles and rapid tool changes. The agility of roller guides, combined with the latest controls, offers essentially unlimited programming capabilities, a stark contrast to the DNC-controlled older machines with limited memory and programming depth.
Cutting-Edge Software & Controls
At Minland Machine, we’re routinely updating our programming software to ensure compatibility and maximize the performance of both box way and roller guide machines. The newer roller guide machines come equipped with state-of-the-art controls that provide expansive programming capabilities, allowing for finer, more intricate work with shallower depths of cut. This technological advancement is complemented by our use of M-code and G-code across all our machines, ensuring a uniform and efficient operating standard.
Advancements in Tooling & Equipment
The evolution of machining has brought about significant improvements in tool life, chip evacuation and feed rates, thanks in part to through-spindle coolant systems. Unlike traditional coolant lines that only target the exterior of tools, the latest tooling features internal channels that distribute coolant directly to the cutting surface, enhancing performance and extending tool life. This advancement is a standard across our new pieces of equipment, including a Doosan mill from Dynamic Machine.
Precision & Range: The Mills
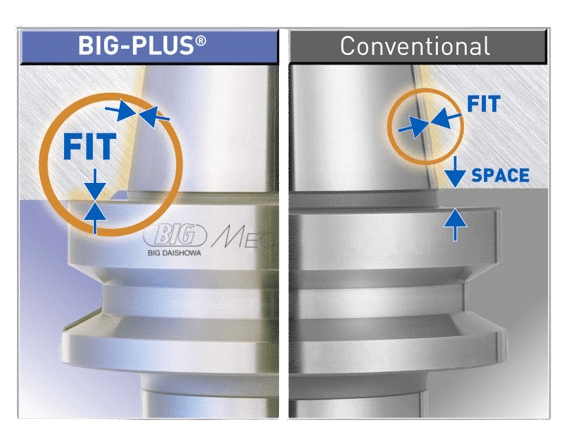
When considering the scope of your projects, the physical capabilities of our milling machines, including our 80×36 mill with 80 inches of X travel and 36 inches of Y travel, provide a glimpse into the many possibilities. The choice between a CAT 40, CAT 50 and CAT 50 BIG-PLUS spindle allows customers to select the perfect balance between heavy-duty performance and precision.
How Minland Machine Enhances Your Manufacturing
Whether you require the heavy-duty capabilities of our box way machines or the high-speed precision of our roller guide systems, we have the technology and expertise to elevate your manufacturing processes.
Our team is devoted to ensuring you leverage the full potential of our advanced software, industry-leading tooling and expansive range of equipment to meet and exceed your production goals.
Let us help you navigate the complexities of modern machining with ease and confidence, turning your visions into reality. Contact Minland Machine today with your next project’s challenges and learn more about how we can help!