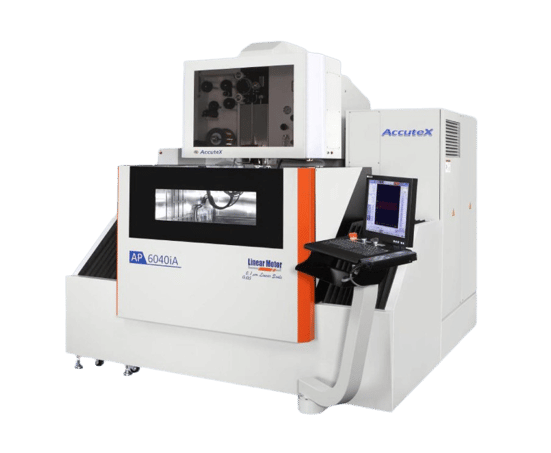
Minland Machine is a full-service CNC machine and job shop facility that has been in business for over 35 years. Utilizing the latest in CAD/CAM software, Minland specializes in the manufacturing of automated extrusion benders and punching feeders for the window extrusion industry. We offer prototyping, fixturing, electrical and mechanical engineering. We also custom design and build computerized and automated machines for specific applications.
In order to produce high-quality results for our clients, we utilize a variety of equipment, including the Accutex AP-6040A Linear Motor Wire EDM. In this blog post, we’ll be taking a closer look at this type of EDM equipment and how it can benefit your business.
What is EDM Equipment?
EDM equipment, or electrical discharge machining equipment, uses a controlled electrical spark to remove material from a workpiece. This process is non-contact, which means there is no direct contact between the tool and the workpiece. This lack of contact prevents tool wear and allows for extremely precise cuts.
EDM equipment can be applied in a variety of industries, including aerospace, automotive, medical and die/mold making. The most common types of EDM equipment are wire cutters and sinkers. Wire cutters use a thin wire electrode to cut shapes into conductive materials like carbon steel, brass, aluminum and copper. Sinkers use electrodes to create cavities in non-conductive materials like tungsten carbide, ceramic, glass and graphite.
How Does It Work?
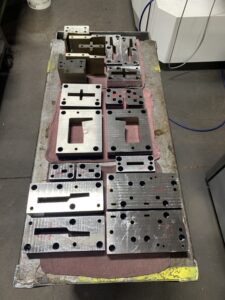
Wire cutters work by dipping a thin wire electrode into a tank of dielectric fluid. The wire electrode is connected to a power supply that sends electrical pulses through the wire. As the electrical pulses pass through the wire electrode, they ionize the dielectric fluid around the electrode. This ionization creates plasma — a conductive path of electrons between the electrode and the workpiece.
The plasma channel conducts electrical current from the electrode to the workpiece, which generates heat. The heat causes local melting and vaporization at the point of contact between the plasma channel and the workpiece surface. This melts away tiny pieces of material from the workpiece surface — the chips — and flushes them away with the dielectric fluid flow.
As more material is removed from the workpiece surface, the shape of the desired cavity starts to take form. When the desired shape has been achieved, the power supply is turned off and dielectric fluid flow is stopped. The melted material cools and solidifies, leaving behind a precisely machined cavity in the workpiece surface.
Benefits of Using EDM Equipment
There are many benefits of using EDM equipment, including:
• Precision: EDM machines can achieve incredible levels of precision, making them ideal for creating small or intricate parts.
• Versatility: Thanks to their ability to work with a variety of materials, EDM machines are uniquely versatile and can be used for a wide range of applications.
• Speed: EDM machines can operate quickly and efficiently, meaning your project can be completed in a timely manner.
Why Minland Machine?
At Minland Machine, we pride ourselves on our ability to take on even the most challenging CNC projects. Our team of experienced professionals has extensive knowledge of all types of CNC equipment, including EDM machines. We use only the latest in CAD/CAM software so that we can provide our clients with precise results that meet their unique specifications.
Wire cut EDM equipment provides many benefits for businesses that require precise cuts on their projects. The non-contact nature of this type of EDM equipment prevents tool wear while still allowing for accurate results every time.
If you’re looking for quality results on your next project, consider utilizing Minland Machine’s top-of-the-line Accutex AP-6040A Linear Motor Wire EDM equipment on your next project. Contact us today to learn more about our services or request a quote for your next project!